Floor Screeding Chalk Farm Greater London (NW1): Doing improvement work on your home in Chalk Farm? Are you fixing uneven flooring in your living space, or infusing new life into a damp and dingy basement? A competent floor screeding specialist can be your secret weapon. They create the perfect starting point: a smooth, level foundation upon which your dream floor - be it carpet, wood or tile - comes to life. Durability meets aesthetics! This important step isn't just about visual appeal; it guarantees the long-term robustness of your entire floor structure, ensuring years of enjoyment. Before you delve into floor coverings, make an investment in success by securing a specialist floor screeding foundation!
FLOOR SCREEDING CONTRACTORS CHALK FARM
A reputable screeding firm in Chalk Farm will have all the know-how and experience to help you achieve a perfectly finished floor in whatever shape or size of room you are renovating. After a painstaking evaluation of your screeding project, they will be able to advise you on which method of laying is most suitable for your floor, and what is the best kind of screed.
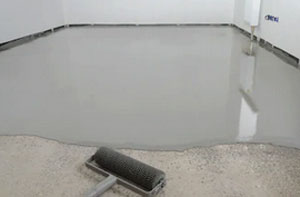
It may be necessary, according to the intended use of the room, for a structural engineering survey to abide by building regulations on flex strength, load requirements and point loadings of the screed floor.
The training and skills that a screeding contractor brings to your project should guarantee a high quality end result and help in extending the life of your floors. There are numerous types of screed and choosing the right mix and installation approach is vital if you are to create a high quality floor that is long-lasting and fit for purpose.
There are numerous screeding contractors in the Chalk Farm area so if possible get multiple quotations for your screeding project before choosing a contractor and know to what standard of finish it's for. The SR (Surface Regularity) finish is the figure to look for when getting a quote from your Chalk Farm screeding contractor. Each of the three SR levels offer different standards of finish, with SR1 being the highest quality, with the lowest amount of deviation over the surface area. This means you might have to correct any patches that could cause problems when putting down your final flooring solution.
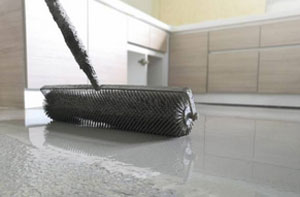
The regulations and guidelines specified in the British Standards BS8204 have to be followed by all Chalk Farm floor screeding contractors and they must also hold accreditation with the manufacturers of any specialist screeding materials (Gypsol, Cemfloor, Flowcrete etc.) to substantiate their competence and safe working practices. A company holding such accreditations demonstrates they've been trained and assessed in using these products and can deliver a high quality standard in all areas of their installation.
For larger screeding projects in schools, hospitals, warehouses, shops, pubs and factories, skilled Chalk Farm commercial screeders will be needed.
TYPES OF SCREED
Standard Screeds - This is okay for standard domestic usage and is a mix of cement and sand. The ratios involved are five parts sand to one part cement. After laying a standard screed sets at a rate of just 1mm/day.
Liquid or Self-Levelling Screeds - Used to produce a high quality finish, especially where SR1 levels are required, by a latex and cement formula. It is mostly needed to provide a clean, smooth floor over the top of a damaged or poor quality substrate and enables all types of flooring materials to be used. These can be as little as 1mm thick, and because of the latex polymers, will still provide high strength.
Fibre Reinforced Screed - Used with underfloor heating and is the advised choice in these projects. The improved flexibility and strength offered by the fibres in the screed help protect the flooring from thermal cracking and shrinkage. At roughly 1mm per day, it has the same curing rate to standard screed.
Industrial and Heavy Duty Screed - A screed designed for high load and heavy traffic areas where the maximum possible durability and strength is very important.
Fast Drying and Advanced Drying Screeds - If you have to use the area as quickly as possible a fast drying screed can be utilised. Drying out at a rate of 3-7mm, depending on the mixture, they're generally a fibre reinforced kind of screed and are ideal for flooring projects which have tight deadlines.
Polymer Screeds - A high strength flooring solution where a reduced thickness is required. Polymer screeds are available from many screed manufacturers and due to their different chemical compositions have distinct drying times for each product.
SCREEDING PREPARATION AND INSTALLATION
To make certain that the screeding is of a high quality finish that's hard wearing and durable, time should be spent on carefully preparing the area prior to any screeding material being laid. It is crucial that all contaminants such as grease, paint, loose debris or oil is eradicated from the base before pouring any screed, because these can affect the bonding process that a good quality floor screed requires.
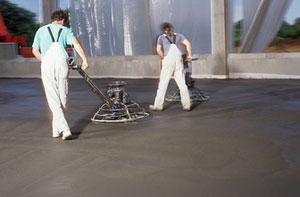
If any cleaning products were used in this process it's vital to ensure that no residues of soaps or other cleaning products are left on the surface and it's permitted to dry out naturally. It is necessary to mend any cracks in the base to avoid them being mirrored and "travelling" upwards into the freshly screeded floor. During a site survey your Chalk Farm screeding installer will notice what preparation work is needed before any actual screeding work commences.
A damp proof membrane (DPM) will be applied after the preparation work has been concluded to stop ground moisture getting into the screed and floor materials. Different gauges of specialised polythene may be used as a damp proof membrane and also act as a barrier for the screed and any insulation panels.
If your property is located in an area where radon gas is present an additional barrier layer is required to stop radon gas from entering. An air-tight membrane might be sufficient in areas with relatively low levels of radon, but in more extreme situations there may need to be a more sophisticated extraction system to block any harmful radon gases.
As soon as these stages have been completed the screeders will apply a sealant or primer to the prepared floor base. These primers and sealers will make certain that the screed bonds properly to the floor base and help achieve a top quality finished floor. These materials require trained contractors to apply them in the right proportions by using custom-made equipment, such as airless sprays.
Before the screeding is poured, any under floor heating (if required) will now be installed. Insulation panels can be put in position and the heating pipes and cabling will be firmly attached to prevent any movement while the screed is being applied. Under floor heating is one of the most effective ways to heat a room and a skillfully installed system should produce even warmth across the floor area.
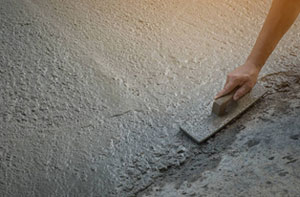
Naturally, if you're not putting in under floor heating, you simply ignore this step and get on with applying the floor screed. Your use of the room will help your screeding contractor on which kind of floor screed is best for your requirements. After the pouring of the screed there is a minimum twenty four hours (for advanced and quick drying screeds) before you are able to walk on the surface, and a 72 hours minimum setting period for any floor material installations. If you're using heavy duty or standard screeds the drying time is longer and the manufacturer's guidelines must be adhered to so as to get the best finish for your floor.
You can test the SR standard of the finished screed as soon as it is set enough to walk on. The test involves the use of a 2 metre straight edge laid on the surface and any variations from true are calculated.
- SR1 - Disparities of three millimetres or less being measured over the whole floor area shows your screeding to be of the finest quality and is classified as SR1.
- SR2 - If the screeded surface has a deviation from the straight-edge of 5 millimetres or less it is classified as SR2 quality and is the normal standard for commercial and industrial projects.
- SR3 - If the deviation around the room is 10mm or less the screeding quality is specified as SR3 and is suitable for utility and garage areas.
There may also be a requirement for a qualified structural engineer to carry out a soundness test. This assessment will determine the overall strength of the screeded surface and its viability for the intended use. An assessment called the drop hammer test will be performed at several areas on the screed layer and the results recorded. Any screed floor that's got point load requirements must be sanctioned by a certified structural engineer heeding the British Standards BS8204 guidelines. (Tags: Floor Screeding Services Chalk Farm, Floor Screed Chalk Farm, Screeding Chalk Farm, Floor Screeding Chalk Farm).
Screeding is available in Chalk Farm and also nearby in: Falconer Walk, Dartmouth Park, Market Estate, Belsize Park, Hilldrop Estate, Primrose Hill, St John's Wood, Bloomsbury, Kilburn, Barnsbury Estate, Kentish Town, Clerkenwell, Highbury, Marylebone, Archway, Camden Town, and in these postcodes NW3 2DQ, NW3 2DJ, NW1 8HH, NW1 8SY, NW1 8FA, NW1 8HG, NW1 8ST, NW1 8SU, NW1 8DY, and NW1 8DL. Locally based Chalk Farm floor screeders will likely have the postcode NW1 and the dialling code 020. Checking this can confirm that you're accessing local screeding. Chalk Farm home and business owners will be able to utilise these and many other similar services. Home and property owners who need floor screeding estimates can just click on the "Quote" banner.
Screed Reinforcement
The technique for reinforcing concrete screeds using screed reinforcement is implemented to improve their strength and durability. Level surfaces are produced by applying flat, thin layers of concrete to a base layer, known as screeds. Their typical application in building projects is as flooring, although they can also be used as a finishing layer for ceilings and walls.
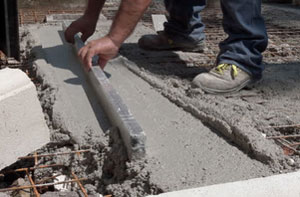
To prevent cracking and increase the strength of the screed, reinforcement materials such as wire, fibres or steel mesh are embedded within the screed mixture during the installation process. The reinforcement of the surface evens out the distribution of load and weight while also increasing its resistance to impact, abrasion and thermal changes.
In addition to improving the screed's durability and strength, screed reinforcement also helps to reduce the risk of shrinkage and cracking caused by changes in humidity or temperature. Even distribution throughout the screed and avoiding displacement over time are dependent on the correct installation of the reinforcement, which is essential. For a long-lasting and reliable surface suitable for various applications, the use of screed reinforcement is essential to maintain the quality and structural integrity of screeds.
Latex Floor Screeds
Before laying final floor coverings, using latex floor screeds to create smooth, level surfaces is a popular option. Flexible and easy to apply, these screeds are created by mixing cement with latex. For use on uneven or cracked floors, they are ideal as the latex ensures the screed adheres well and prevents cracking.
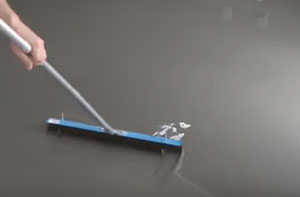
Applying latex floor screeds is an uncomplicated task. Initially, the existing floor needs to be cleaned and primed to guarantee good adhesion. After that, the screed mixture should be poured onto the floor and spread out evenly using a trowel. This results in a smooth, level surface, ready for vinyl, tiles, or other floor coverings, once it has dried.
A notable benefit of latex floor screeds is their short drying time. Unlike traditional screeds that need days to dry, latex screeds are ready to walk on in just a few hours. Given that time is frequently a critical factor, they are an excellent choice for both residential and commercial projects in Chalk Farm. (Latex Floor Screeds)
Granolithic Screeding
Granolithic screeding is a technique used to create a durable and hard-wearing surface, often required in industrial or commercial settings in Chalk Farm. Granolithic screeding is composed of cement, sand, and fine aggregate, like granite or other hard stones, making it stronger and more resilient than standard concrete. For areas exposed to heavy traffic or machinery, granolithic screeding is a great option due to its resistance to wear and tear.
The installation process entails laying the granolithic screed over a prepared base, typically a concrete subfloor. To guarantee a surface that is smooth and even, the screed is thoroughly levelled and compacted, making it suitable for heavy use. With a polished finish, it offers not only durability but also an attractive, smooth surface ideal for high-traffic areas such as warehouses or workshops in Chalk Farm.
Strong and cost-effective, granolithic screeding is esteemed for both its durability and cost-related advantages. Once installed, it demands minimal maintenance and can last for many years, making it an ideal choice for both commercial and industrial spaces. Granolithic screeding offers a long-lasting floor solution, suitable for factories, loading bays, or large residential garages. (Tags: Granolithic Screeding Chalk Farm)
Multi-Coloured Floor Screeds
Multi-coloured floor screeds are a fantastic way to bring both personality and practicality into any environment. These decorative options blend durability with striking design, resulting in a seamless flooring solution that is both tough and visually appealing. Whether you're outfitting commercial spaces, industrial zones, or trendy homes in Chalk Farm, multi-coloured screeds provide a distinctive mix of style and usefulness. Their lively finishes allow for tailored choices, giving you the freedom to reflect your personal style or brand identity through colours and patterns.

The versatility of multi-coloured floor screeds truly sets them apart. Built for durability, they're perfect for handling heavy use in high-traffic areas, while their seamless finish ensures they're easy to clean and maintain. Commercial settings benefit from bold colour options that create striking interiors or distinct zones. At home, softer colours and detailed patterns can transform kitchens, bathrooms, or living rooms into stylish, modern spaces.
Multi-coloured screeds go beyond simple aesthetics; they are a worthwhile investment in lasting quality. With their hard-wearing nature, they're designed to endure even the most challenging environments. Additionally, they can be tailored to meet specific requirements, such as ensuring slip resistance or providing extra protection from spills and chemicals. Whether you're looking to breathe new life into a tired old floor or create a bold design statement, these multi-coloured floor screeds offer a practical and stylish solution for your home or business in Chalk Farm. They exemplify the fusion of functionality and flair, transforming any space into something truly unique. (Tags: Multi-Coloured Floor Screeds Chalk Farm).
Polished Screeds Chalk Farm
Seeking a modern and stylish flooring option, many Chalk Farm home and property owners are turning to polished screeds. Providing a durable and aesthetically pleasing foundation for various living areas, these screeds feature a smooth, trowel-finished surface. Polished to a dazzling sheen, this technique creates a floor that's not only practical but also visually appealing. The process begins with laying a cementitious material.
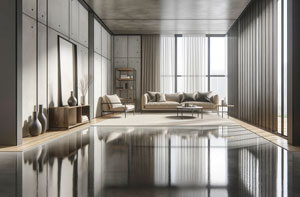
The fact they they require very little upkeep is a major advantage of polished screed floors. Polished screeds do not require frequent waxing or sealing, unlike many conventional flooring alternatives. Offering resistance to allergens and dust due to their seamless surface, polished screeds are a perfect option for allergy and asthma sufferers. Polished screeds are also remarkably wear-resistant, guaranteeing a long lifespan and reducing the frequency and cost of necessary replacements and repairs.
The versatility of polished screed floors is something that property owners in Chalk Farm can also benefit from. With a wide array of colours and finishes at your disposal, polished screeds can be the perfect finishing touch to complement your existing design theme. Polished screeds can enhance the overall appearance of a home, whether one decides on an intricate pattern or a more low-key, minimalist design. Furthermore, the mirror-like surface that they create can enhance the brightness of rooms by maximising natural light, leading to a more welcoming and open atmosphere. (Polished Floor Screeds Chalk Farm)
Screed Floor Removal Chalk Farm
Screed floor removal is an essential process in the realm of construction and renovation, employed to strip away existing screed layers from floor surfaces. This practice is essential for the renovation or upgrading of a floor. It prepares the surface for the new flooring material or other modifications.
Screed floor removal is an intricate task that is best left to skilled contractors who have expertise in this field. Their experience ensures the safe and efficient elimination of the old screeding, paving the way for a fresh start for the floor. This fresh start is significant for upgrades, changes in design or repairs, amongst other things.
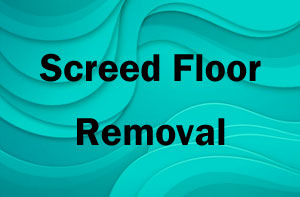
The process of removing floor screed involves the use of specialist equipment and techniques that are tailored to the particular task at hand. The assessment should encompass the screed's thickness, type, and the surface it's being applied onto. Minimal damage to the underlying structure is achieved through careful attention to detail during removal.
An important benefit of removing floor screed is that it gives you the opportunity to deal with any underlying problems that might have developed over time. A thorough examination of the underlayer is possible only after removing the old layer of screed, if it's uneven, damaged, or compromised. Screeding specialists can use this assessment to identify and rectify any structural problems that could affect the installation of new flooring materials.
Furthermore, for the implementation of underfloor heating systems in Chalk Farm, removing the screed floor is a major preliminary step. The process of removing the pre-existing screed enables contractors to prepare a surface that is level, clean, and favourable for heating element installation. This approach facilitates an effective and efficient underfloor heating system, thereby increasing the space's energy efficiency and comfort.
From a sustainability perspective, screed floor removal embodies the ideals of waste reduction and reusability. Repurposing or recycling this material creates a circular economy within construction, significantly reducing the environmental impact of its removal.
To summarise, within the field of renovation and construction, the removal of screed floors is an intricate and crucial process. Navigating the complexities of removing old layers of screed while ensuring the integrity and safety of the base structure requires the expertise of professional contractors. By enabling a fresh start for the floor, screed floor removal contributes to the creation of efficient, durable, and visually pleasing flooring solutions in a number of different commercial and residential settings in Chalk Farm. (27543 - Screed Floor Removal Chalk Farm)
Chalk Farm Screeding Related Tasks
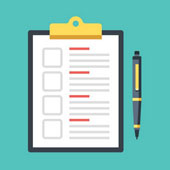
There are a wide range of tasks that can be carried out by your local Chalk Farm floor screeder including bonded screed, commercial screeding, factory floor screeding, screeding repairs, coloured floor screeding in Chalk Farm, screed floor removal, anhydrite floor screeding in Chalk Farm, concrete pumping, screed reinforcement, conservatory floor screeding, concrete screeding, granolithic screed , fibre reinforced screeding, underfloor heating screed, screed surveys & testing, underfloor heating installation, floor noise reduction, floating screed, structural screeds, final floor finishes in Chalk Farm, wet room floors, floor screeding price quotes, resin floor screeds in Chalk Farm, self-levelling floor screeding, garage screeding, decorative floor screeding, sand floor screeding, acid etching concrete, screeded kitchen floors, fast drying screeds, and more floor screeding tasks. These are just an example of the duties that are conducted by those specialising in floor screeding. Chalk Farm providers will keep you informed about their entire range of floor screeding services.
The Tools Needed for Screeding Floors
- Spade
- Measure
- Buckets
- Spirit Level
- Straight Edge
- Knee Protection
- Floor Profile
- Dappling Bar
- Float
- Gloves
- Trowel
Local Screeding Enquiries
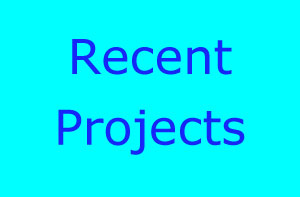
Current floor screeding postings: Jasmine Harrison recently asked for a quotation for screeding a property extension floor in Market Estate. Christina and Christian Rogers recently requested a quotation for screeding a utility room floor in Kilburn. Patrick and Rebecca Carter recently asked for an estimate for screeding the floor of a workshop in Belsize Park. Joshua Price and Sarah Price recently enquired about screeding a basement floor in Hilldrop Estate. Stephanie and Brian Gordon recently requested a quotation for screeding a utility room floor in Highbury. Richard Davies was looking for floor screeders near Clerkenwell. Maria Lee and Jeremy Lee recently asked for an estimate for screeding a lounge and kitchen floor in a detached house in Barnsbury Estate. Steven and Allison Allen recently asked for a quote for installing underfloor heating and screeding a floor in Camden Town. Austin Clark and Allison Clark recently requested a quote for screeding over an old concrete floor in St John's Wood. Mr and Mrs Atkinson recently requested an estimate for screeding the floor of a cellar in Primrose Hill. William Russell and Nicole Russell recently requested a quote for screeding over an old concrete floor in Dartmouth Park. Anna and Tom Rogers recently requested a quotation for screeding a utility room floor in Barnsbury Estate. Benjamin and Samantha Walsh recently asked for an estimate for screeding the floor of a workshop in Kentish Town. All of these local people conducted a search for "floor screeding near me" and located this web page on either Google, Bing or Yahoo.
Floor Screeding Near Chalk Farm
Also find: Marylebone floor screeding, Archway floor screeding, Dartmouth Park floor screeding, Falconer Walk floor screeding, St John's Wood floor screeding, Kilburn floor screeding, Bloomsbury floor screeding, Hilldrop Estate floor screeding, Primrose Hill floor screeding, Belsize Park floor screeding, Highbury floor screeding, Clerkenwell floor screeding, Barnsbury Estate floor screeding, Market Estate floor screeding, Kentish Town floor screeding, Camden Town floor screeding and more. These and other towns and settlements are served by screeding specialists and associated tradesmen and women. These experienced professionals, by virtue of their skills and expertise, are capable of delivering top-notch flooring solutions. In the world of screeding for both commercial and domestic properties, they're highly skilled, guaranteeing fine quality work. By clicking here, local householders can obtain screeding estimates. Do you have floors that need screeding? Don't delay - get a quote today!
Floor Screeding Services Chalk Farm
- Fibre Reinforced Floor Screeding
- Screeding Services
- Domestic Floor Screeding
- Floor Insulation
- Underfloor Heating Installations
- Screeding Advice
- Final Floor Finishes
- Floor Screeding
- Kitchen Screeding
- Fast-Dry Floor Screeding
- Screed After Care
- Floor Levelling
- Polished Screed Floors
- Liquid Screeds
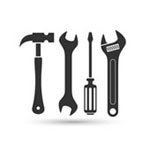
Other Trades Chalk Farm: Okay, so you are currently in search of screeding in Chalk Farm, but you could also require a carpenter in Chalk Farm, a carpet layer in Chalk Farm, a plasterer in Chalk Farm, a general builder in Chalk Farm, parquet flooring in Chalk Farm, garage conversion in Chalk Farm, an electrician in Chalk Farm, a damp proofing specialist in Chalk Farm, a heating engineer in Chalk Farm, a flooring expert in Chalk Farm, a handyperson in Chalk Farm, waste removal in Chalk Farm, an underfloor heating specialist in Chalk Farm, when carrying out any home improvement assignment in Chalk Farm. To make enquiries and get quotes, click on the highlighted links.
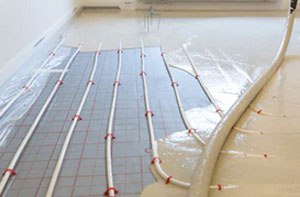
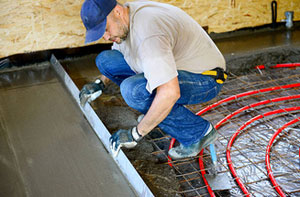
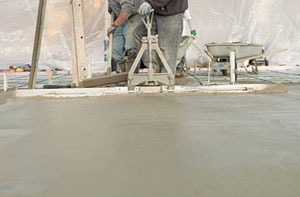
To read local Chalk Farm information click here
More: Floor Screeders, Floor Screeding, Screeding, Decorative Screeding, Screed Floors, Self-Levelling Screeds, Decorative Screeding, Screed Floors, Commercial Screeding, Floor Levelling Services, Self-Levelling Screeds, Floor Screeders, Flooring Contractors, Self-Levelling Screeds, Residential Screeding, Floor Screeders, Screed Floors, Screed Flooring, Floor Screeders, Screeding Specialists, Self-Levelling Screeds, Floor Levelling Services, Commercial Screeding, Floor Screeding, Commercial Screeding, Screeding, Decorative Screeding, Screed Reinforcement, Polished Screeding, Decorative Screeding, Coloured Screeding, Screeding, Screeding Specialists, Screeding, Cheap Driveways, Driveways, Concrete Driveway Contractors.
Floor screeding in NW1 area, phone code 020.
TOP - Floor Screeding Chalk Farm
Floor Levelling Chalk Farm - Industrial Screeding Chalk Farm - Floor Screeding Contractors Chalk Farm - Screeding Services Chalk Farm - Floor Screeders Chalk Farm - Self-Levelling Screeding Chalk Farm - Underfloor Heating Chalk Farm - Floor Screeding Chalk Farm - Domestic Screeding Chalk Farm