Floor Screeding Services: When it comes to your UK home or business premises, a skilled floor screeding professional can assist with a range of services. They can install underfloor heating, level out damaged or uneven floors, and contribute to renovations when necessary. Achieving a flat surface is crucial before applying the final floor covering, whether it's carpet, wood, or tiles. This is where floor screeding plays a vital role. If durability is a priority for your floors, then a well-executed floor screed is one of the most critical factors to consider in any renovation or construction project.
FLOOR SCREEDING CONTRACTORS UK
Regardless of the size of your room, whether it's compact or spacious, that needs to be levelled, an experienced screeding contractor within the UK is equipped with the essential tools, proficiency, and understanding required to provide a service of outstanding quality. They are well-prepared to offer guidance in choosing the most suitable screed type for your particular project, along with providing valuable insights into the most effective methods of application and installation. You can be confident that their extensive expertise will guarantee you receive unparalleled advice and a service that is customised meticulously to meet your unique requirements.
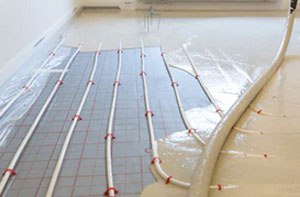
Depending on the intended usage of the area, it might be essential to conduct a structural engineering survey to comply with building regulations pertaining to the flex strength, load-bearing capacity, and point loadings of the screed floor. This ensures that the floor can withstand the expected loads and meet the necessary safety standards. Adhering to these regulations is crucial to guarantee the structural integrity and durability of the screed floor, providing a safe and reliable surface for its intended purpose.
Engaging the expertise of a qualified screeding specialist for your project ensures a superior end result and enhances the longevity of your flooring. Their skills and training contribute significantly to achieving a high-quality outcome. Equally important is the correct composition of the screed mixture and the meticulous methods employed during its application. These factors play a crucial role in guaranteeing the long-lasting durability of your floor surface. By prioritising the skills of a qualified screeding specialist and adhering to proper mixing and installation techniques, you can be confident in the lasting quality and resilience of your floor.
When searching for screeding companies in and around the UK, it is advisable to obtain multiple price quotes for your project. It is essential to understand the desired standard of finish before making a decision. Quotes are often based on a measurement known as Surface Regularity (SR) number. Opting for SR2 or SR3 may be more cost-effective, but it could result in a floor screeding finish that contains errors and deviations. On the other hand, choosing SR1 ensures a flawless finish. It is crucial to note that imperfections in screeding can lead to difficulties when laying flooring, including indentations, ridges, and flat spots on the surface.
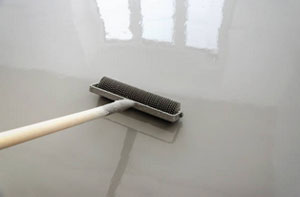
In order to comply with British Standards (BS8204), it is mandatory for all UK screeding companies to observe these guidelines. Additionally, it is recommended that they possess accreditation from manufacturers of screeding equipment and materials, such as Gypsol, Cemfloor, and Flowcrete. The accreditation serves as evidence that the contractors have undergone training and evaluation in the proper utilization of these products. By holding such accreditation, contractors demonstrate their ability to deliver a high-quality service across all aspects of the installation process. This ensures that customers can rely on their expertise and expect a top-notch service from knowledgeable professionals who are well-versed in the use of the latest screeding materials and equipment. By working with accredited contractors, clients can have peace of mind knowing that they are receiving a superior level of service from UK screeding companies that prioritize quality and adhere to industry standards.
UK commercial screeders might be involved in screeding floors in factories, hospitals, shops, warehouses, pubs and schools.
TYPES OF SCREED
Standard Screeds - A mix of sand and cement which is ideal for normal residential use. 5 parts sand to 1 part cement is the usual mix for standard screed. The standard flooring screed will dry at a rate of 1mm thickness each day.
Liquid or Self-Levelling Screeds - The combination of latex and cement creates a superior material capable of achieving the highest standard SR1 finish. This particular type of screed is especially valuable when constructing a high-quality floor over a subpar or damaged substrate. It results in a surface that serves as an ideal foundation for various flooring materials. Despite being only one millimetre thick, the presence of latex polymers within the screed imparts remarkable strength, rendering it suitable for a wide range of applications. This latex and cement screed ensures a durable and resilient surface that can withstand the demands of diverse uses, providing a reliable and long-lasting solution.
Industrial and Heavy Duty Screed - In areas where high traffic or heavy floor loading is anticipated, the use of heavy-duty screeds becomes imperative to achieve maximum strength and durability. These specialized screeds are specifically designed to withstand the demands of such environments. With their enhanced strength properties, heavy-duty screeds provide a robust and resilient surface capable of enduring heavy foot traffic and substantial loads. By utilizing these screeds, the floor can maintain its structural integrity and withstand the challenges posed by demanding conditions. Whether it's in commercial, industrial, or high-traffic residential settings, heavy-duty screeds offer a reliable solution to ensure long-lasting performance and durability.
Fibre Reinforced Screed - Fibre Reinforced Screed is the preferred option among professional contractors, particularly when working with underfloor heating systems. This choice is primarily driven by the enhanced strength it offers, as well as its ability to provide protection against thermal cracking and shrinkage. The inclusion of special fibres within the screed mix contributes to these advantages. Additionally, this type of screed has the benefit of drying at a consistent rate of 1mm per day, similar to that of a standard screed. This feature ensures a controlled and predictable drying process, allowing for efficient project planning and execution. With its superior properties and compatibility with underfloor heating, Fibre Reinforced Screed remains a popular and reliable choice for contractors seeking optimal performance and durability.
Advanced Drying and Fast Drying Screeds - In situations where the area in question needs to be utilized as soon as possible, the use of a fast-drying screed becomes necessary. Typically, fast-drying screeds are fibre reinforced and have a drying rate ranging between 3-7mm per day. These screeds are specifically employed in time-critical flooring projects where rapid completion is of utmost importance. The incorporation of fibres enhances their strength and performance, while the accelerated drying process allows for quicker access to the area. By opting for a fast-drying screed, project timelines can be expedited, enabling prompt usage of the space without compromising on the quality or durability of the floor finish.
Polymer Screeds - For situations that demand a reduced screed thickness while still requiring an exceptionally strong flooring solution, polymer screeds offer an ideal choice. These screeds, manufactured by various companies, possess distinct chemical compositions, resulting in specific setting times for each product. The advantage of polymer screeds lies in their high strength properties, allowing for thinner application without compromising durability. They provide a reliable and robust surface for a range of applications. The specific setting times of polymer screeds ensure proper curing and drying, facilitating efficient project planning and execution. Whether for commercial, industrial, or residential projects, polymer screeds offer a versatile flooring solution that meets strength requirements while accommodating the need for reduced screed thickness.
SCREEDING PREPARATION AND INSTALLATION
In order to ensure a high-quality and durable screed flooring, screeding installers must thoroughly prepare all areas before commencing any other work. This preparation phase is crucial to create an optimal surface for screed application. It is imperative to remove any contaminants, including oil, debris, paint, or grease, from the floor prior to pouring the screed. These substances can adversely affect the adhesion capability that a top-quality floor screed necessitates. By eradicating these contaminants, the screed can bond effectively with the substrate, ensuring a robust and long-lasting flooring system. The meticulous removal of such impurities guarantees the integrity and performance of the screed, providing a reliable and enduring foundation for the chosen floor finish.
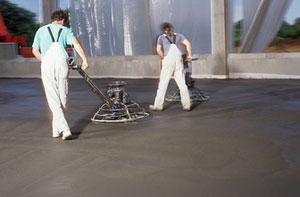
After using cleaning products, it is crucial to thoroughly eliminate any traces of soap or similar substances and allow the floor surface to dry naturally. It is of utmost importance to address any crevices or cracks present on the surface to prevent them from being replicated or propagating upward into the newly screeded floor. Conducting a site survey enables your UK screeding company to identify and address these preparation requirements before proceeding with the screeding process. By proactively addressing these issues, potential problems are mitigated, ensuring a seamless and durable screed installation. This comprehensive approach guarantees that the floor surface is properly prepared, minimising the risk of future issues and providing a solid foundation for the successful pouring of the screed.
Prior to the application of any screed, it is essential to install a damp proof membrane (DPM) to safeguard both the screed and the final flooring from moisture. The DPM consists of a durable polythene sheeting, typically of considerable thickness. Multiple layers of DPM may be employed to serve as an effective moisture barrier and provide an insulating layer against air for the screed. This protective measure prevents dampness from penetrating the screed and subsequently affecting the integrity of the final flooring. By incorporating a DPM, the screed remains shielded from moisture-related issues, ensuring its longevity and maintaining the quality of the overall flooring system.
For properties located in areas where radon gas is present, an additional barrier layer is necessary to prevent its entry. In locations with low radon measurements, an air-tight membrane might suffice as a preventive measure. However, in more severe cases, a more intricate extraction and ventilation system may be required to effectively block the infiltration of harmful radon gases. This comprehensive approach ensures the safety and well-being of occupants by minimizing their exposure to radon. By implementing the appropriate barrier layer or employing advanced extraction and ventilation systems, the risk associated with radon gas can be mitigated, creating a healthier indoor environment. It is crucial to assess the radon levels and consult with experts to determine the most suitable approach for effectively addressing radon gas in your property.
Once the base has been thoroughly prepared and all DPMs (damp proof membranes) are in place, the next step involves applying a sealer or primer. These essential coatings serve two purposes: ensuring a strong bond between the screed and the base surface, and facilitating the achievement of a high-quality finished floor. To apply the sealant or primer, certified screeding companies in the UK employ equipment such as airless sprays. It is crucial for these companies to follow the manufacturer's guidelines and safety advice to ensure proper application. By adhering to the recommended procedures, the sealant or primer can be effectively applied, promoting a secure bond and enhancing the overall quality of the final floor. This attention to detail and adherence to industry standards contribute to the success and longevity of the screeding project.
Prior to the application of screed, it is necessary to install any underfloor heating system. This involves securely attaching the cabling and heating pipes to insulation panels, ensuring they are positioned correctly and preventing any movement. Underfloor heating is widely regarded as one of the most efficient methods to heat a room, and a professionally installed system ensures even warmth throughout the entire floor area. The proper installation of the underfloor heating system guarantees optimal performance and comfort. By securely fixing the cabling and pipes to the insulation panels, potential issues such as displacement or misalignment are prevented. This meticulous approach ensures that the underfloor heating system functions effectively, providing consistent warmth and enhancing the overall comfort of the space.
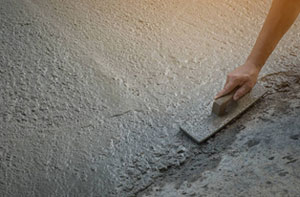
After the necessary preparations, the screed is mixed and prepared on-site, ready to be spread onto the base surface. The choice of screeding type will be determined by the specific requirements of the room. It is important to note that even quick-drying screeds require a minimum of twenty-four hours before any walking activity can take place on the screeded surface, and a minimum of three days before floor coverings can be installed. Adhering to these waiting periods is crucial to achieve a properly finished and long-lasting floor surface. It is essential to follow the manufacturer's guidelines, especially for heavy-duty and standard screeds, as the waiting period may be extended to ensure the desired durability and quality of the finished floor. By respecting these guidelines, the screeded surface can properly cure, allowing for the successful installation of floor coverings and ensuring a robust and reliable final result.
Once the screed has solidified sufficiently for walking, you have the option to test the Surface Regularity (SR) standard of the finished screed. The SR test involves using a two-meter long straight-edge to assess the surface for any irregularities or deviations. By carefully running the straight-edge across the screeded surface, you can identify any variations or inconsistencies in its levelness. This test allows you to ensure that the screeded surface meets the required SR standard, indicating a smooth and even floor finish. Conducting the SR test promptly after the screed has solidified allows for early detection of any potential issues, providing an opportunity to address them before proceeding with the installation of floor coverings. It is an important quality control measure that contributes to achieving a high-quality and visually appealing finished floor.
- SR1 - If disparities of 3mm or less are measured across the entire floor area, it indicates that your screeding has achieved the highest quality and is classified as SR1. This level of precision and uniformity signifies an exceptional standard of screeding workmanship. With such minimal deviations, the screeded surface showcases a flawlessly level and even finish. Achieving an SR1 classification is a testament to the meticulous attention to detail and expertise of the screeding professionals involved in the project. This top-tier quality guarantees a visually pleasing and functionally reliable floor surface that meets the highest industry standards. The SR1 classification serves as a mark of excellence, demonstrating that the screeded floor surpasses expectations in terms of smoothness, levelness, and overall quality.
- SR2 - For commercial and industrial projects, the SR2 classification is typically applicable to standard floors. With SR2, it is permissible for the surface to deviate from the straight-edge by as much as 5 millimetres. This classification recognizes that certain variations within this range are acceptable for commercial and industrial flooring applications. While the tolerance for deviations is slightly higher compared to SR1, an SR2 classification still ensures a satisfactory level of smoothness and evenness for normal flooring requirements in these sectors. It is important to consider the specific needs and expectations of the project when determining the appropriate SR classification. By adhering to the guidelines associated with SR2, contractors can deliver fit-for-purpose flooring solutions that meet the necessary standards and provide functional, visually appealing results.
- SR3 - In utility floors where the aesthetic finish is relatively unimportant, the SR3 standard is commonly employed. With SR3, the acceptable deviation measurement from the straight-edge can be up to 10mm. This classification recognizes that utility floors prioritize functionality over visual appearance. While the permissible deviation is higher compared to SR1 and SR2, it still ensures a reasonably level and even surface suitable for practical purposes. Utility floors, such as those found in industrial or storage areas, often prioritize load-bearing capacity and durability over cosmetic perfection. By adhering to the SR3 standard, contractors can deliver fit-for-purpose flooring solutions that meet the functional requirements of utility spaces while considering the cost-effectiveness and efficiency of the project.
In some instances, it may be necessary to enlist the services of a qualified structural engineer for conducting an in-depth soundness assessment. This crucial examination is designed to ascertain the screed's structural integrity and its appropriateness for the intended application. A key component of the soundness test is the "drop hammer test," which measures various attributes of the screed's durability and strength. Given the necessity for specialised testing and measurement apparatus, such evaluations should exclusively be carried out by a competent structural engineer who is compliant with British Standards BS8204. The involvement of a structural engineer not only ensures a meticulous inspection of the screed's robustness but also provides essential insights into its performance traits. This detailed evaluation plays a pivotal role in determining the overall quality and fitness of the screeded surface, ensuring its durability and long-term performance. (Tags: Floor Screeding Services UK, Floor Screed UK, Floor Screeding UK, Screeding UK).
Latex Floor Screeds UK
When seeking greater flexibility in your flooring surface, you'll discover that utilising a latex self-leveling screed offers an ideal solution. Latex floor screeds typically consist of two components: a liquid latex container and a bag of cement powder. The liquid latex serves as a substitute for traditional water in the screed mixture, providing enhanced flexibility and faster drying properties compared to conventional screeds.
Designed for the purpose of smoothing subfloors, this latex compound creates an excellent foundation for the installation of your chosen final floor coverings. It is a versatile option, suitable for application on various subfloor materials such as quarry tiles, concrete, sand/cement, asphalt, and wood. The result is a resilient and impeccably smooth surface, perfect for securely adhering flooring materials. Even in scenarios where there might be subfloor movement, this type of floor screed ensures a crack-free, flexible finish that stands the test of time.
In cases where a "floating" screed is required, meaning it is being applied over a layer of either thermal or acoustic insulation, it may be necessary to achieve screed depths ranging from 50mm to 75mm. It's worth noting that latex screeds are not suitable for this particular application.
Granolithic Screeding
Granolithic screeding is a specialised technique used in construction and flooring that involves creating a highly durable and robust surface. This screeding method is particularly favoured for areas subjected to heavy foot traffic, industrial applications, and outdoor spaces due to its exceptional strength and resilience.
To create a granolithic screed, a mixture of cement, aggregates (such as granite or marble chips), and sometimes additives like latex is prepared. The proportions of these components are crucial to achieving the desired level of strength and durability. This mixture is then expertly applied and finished by skilled tradespeople. The result is a surface that is not only visually appealing but also incredibly tough and long-lasting.
One of the key advantages of granolithic screeding is its ability to withstand heavy loads and high levels of wear and tear. This makes it a popular choice for commercial and industrial flooring, car parks, and areas where heavy machinery may be used. Additionally, granolithic screeding is resistant to abrasion, chemicals, and weathering, making it suitable for both indoor and outdoor applications.
Furthermore, granolithic screeds can be customised to achieve different textures and finishes, allowing for aesthetic versatility. While it may require skilled labour and precise craftsmanship, the investment in granolithic screeding pays off in terms of durability and longevity, making it an excellent choice for demanding environments.... READ MORE.
Multi-Coloured Floor Screeds
Multi-coloured floor screeds are an exciting and versatile flooring option that allows you to infuse vibrant and customized designs into your spaces. These screeds are typically composed of a blend of pigmented resin materials and aggregates, offering a broad spectrum of colours and finishes to choose from. They provide not only aesthetic appeal but also durability and functionality.
One of the key advantages of multi-coloured floor screeds is their ability to create visually stunning patterns, logos, or graphics in commercial and residential settings. They are often used in retail spaces, showrooms, and even homes to make a bold statement or enhance branding.
Additionally, these floor screeds are easy to clean and maintain, making them suitable for high-traffic areas. They are also seamless and resistant to wear, chemicals, and abrasions, ensuring a long-lasting and attractive flooring solution.
Incorporating multi-coloured floor screeds into your design can transform your space, adding personality, vibrancy, and a unique touch to your interior or commercial setting
What Does Screeding a Floor Involve?
Screeding a floor involves the process of creating a smooth, level, and flat surface by applying a layer of screed over the base floor. Here are the main steps involved in screeding a floor:
- Base Floor Preparation: The base floor needs to be thoroughly cleaned, ensuring it is free from dust, debris, and any loose materials. It should also be dry and structurally sound. Any irregularities or unevenness in the base floor should be addressed before proceeding with the screeding process.
- Mixing the Screed: The screed mixture is prepared by combining cement, sand, and water in the appropriate proportions. The mixing can be done manually by hand or using a mechanical mixer, depending on the scale of the project. It is crucial to achieve a consistent and smooth mixture without any lumps or clumps.
- Pouring the Screed: Once the screed mixture is ready, it is poured onto the base floor. It is essential to work quickly and efficiently during this step to ensure even distribution and prevent the screed from drying out before it can be leveled.
- Leveling and Smoothing: The screed is spread evenly across the floor using a trowel or a straight edge. It is then leveled and smoothed out to create a flat and even surface. A screed board or a leveling tool is typically used to achieve this, with attention given to eliminating any high spots or depressions.
- Drying and Curing: After screeding, the floor needs sufficient time to dry and cure. The drying time can vary depending on factors such as the thickness of the screed, environmental conditions, and the type of screed used. It is important to follow the manufacturer's recommendations for drying and curing times to ensure proper setting and strength development.
- Surface Finishing (Optional): Depending on the desired floor finish, additional steps may be required for surface finishing. This can include techniques such as sealing, polishing, or applying a specific coating to enhance the appearance and durability of the screeded floor.
It is worth noting that screeding a floor is a skilled task that requires experience and expertise. Hiring a professional screeding contractor is recommended to ensure a high-quality and successful outcome. They will have the knowledge, tools, and techniques to carry out the screeding process effectively, resulting in a level and durable floor surface ready for the installation of various floor finishes.
Related Tasks
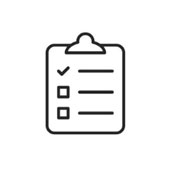
There are a wide array of tasks that can be completed by your local UK floor screeder including screeding price quotes, professional floor levelling services in the UK, bathroom floors, bonded screed, floor screeding tools UK, floor noise reduction, screed reinforcement, coloured floor screeding UK, resin floor screeding UK, sand screeding, flow screeding UK, basement floor screeding, underfloor heating screeds, bonded concrete floor screeding, hospital floor screeding, underfloor heating installations, concrete screeds, floor screeding, damp proof membranes, screeding repairs in the UK, floor resurfacing UK, final floor finishes, substrate floor preparation UK, fast drying or accelerated floor screeds, cheap floor screeding, granolithic floor screed, floor levelling, polished screed flooring, screed testing in the UK, acoustic flooring in the UK, and lots more floor screeding tasks. These are just a handful of the activities that are accomplished by those installing floor screeding. UK specialists will keep you informed about their entire range of services.
Floor Screeding Services UK
- UK Floor Levelling
- UK Floor Screeding Advice
- UK Screeding Services
- UK Residential Floor Screeding
- UK Underfloor Heating Installation
- UK Floor Screeding
- UK Floor Damp Proofing
- UK Cheap Screeding
- UK Floor Insulation
- UK Liquid Screeds
- UK Screed Calculator Service
- UK Fibre Reinforced Screeding
- UK Polished Screed Floors
- UK Commercial Floor Screeding
Other Useful Trades in the UK
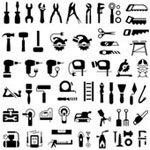
Needless to say, whenever you are doing home renovations in the UK, you'll probably need all types of different tradespeople and as well as a floor screeder in the UK, you may also need solid wood flooring in the UK, a bricklayer in the UK, an electrician in the UK, a carpet fitter in the UK, linoleum flooring in the UK, a plasterer in the UK, a building contractor in the UK, a heating engineer in the UK, a floor tiler in the UK, an underfloor heating specialist in the UK, waste removal in the UK, a handyman in the UK, a carpenter in the UK, a plumber in the UK, and other different UK tradesmen.
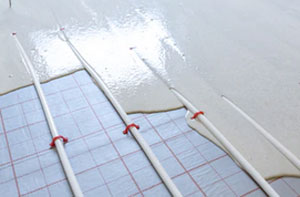
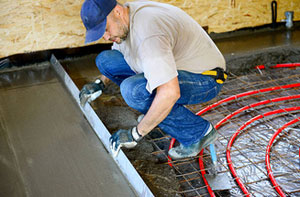
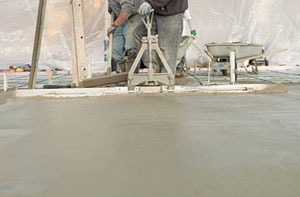
More UK floor screeders: Lancashire, Staffordshire, Lincolnshire, Leicestershire, Suffolk, Northamptonshire, Buckinghamshire.
Floor Screeders - Screeding Specialists - Self-Levelling Screeds - Domestic Screeding - Commercial Screeding - Screeding Services - Floor Screeding Near Me